The Next Dimension
We meet Matt Watkins from Special Studio and hear how the Tauranga-based company is transforming waste into homewares with 3D printing.
At Special Studio, Matt Watkins reimagines a future for plastic with 3D printing — taking waste and transforming it into objects for the home, with the hope of one day printing the home itself.
For those of you who may be a little foggy on the capabilities of a 3D printer, seeing the creation
of a vase made from recycled plastic at Special Studio, a designer homeware brand operating
from Tauranga’s Basestation, certainly brings it to life.
Viewing a 3D printer in action as it slowly responds to a pre-programmed design, a filament of material wound precisely into a templated form, may bring a dawning of comprehension around
how prosthetic limbs and other body parts have become a reality using 3D printing technology.
Now, the ability exists to create an ever-increasing range of items that have previously had a long waiting list, an unachievable price tag or other obstacle.
%20(1).jpg)
One Earth Technology is the parent company for Special Studio and provides an avenue to find
ways of creating value from waste. The 3D printing system allows the processing of waste plastic materials into stylish, one-off home and office wares for a discerning retail market — wastepaper baskets, vases and multi-purpose containers are available to purchase on the Special Studio
website, with commissions welcomed.
The intent of owner/designer Matt Watkins is to harness the abundant potential of 3D printing by transforming plastic waste into desirable objects — filling a niche in the market for larger objects
such as furniture, and eventually focusing residential and even naval architecture. He sees Special Studio as an opportunity to fine-tune techniques and products, develop IP in areas such as material processing and additive manufacturing techniques, and also create new materials and composites with a view to a bigger goal... “Affordable housing is always going to be a necessity, and it’s something which can be achieved using composite materials and 3D printing. These materials
add structural integrity to the build and might include things like wood and ceramic dust, recycled concrete and other things that contribute to the weight, strength and finish of a 3D printed object
— which hopefully one day includes buildings,” Matt explains.
Matt will be known to many from his years at the Mount Surf Shop. He is one of those people who
has an inherently enquiring mind, and his constant desire to seek answers to problems has led him
to create a range of solutions. This talent saw Matt design a software-hardware product for DJs called SoundSwitch. It’s a digital lighting workstation and hardware solution for connecting DJ software
and DMX lighting — it was bought by American-based multinational company inMusic, which now employs over 50 people in Auckland and Tauranga. Matt still works a full-time role for the company, moonlighting for his passion project — 3D printing. He describes his field of work as “material science”, and says, “I believe this is one of the most underrated areas being studied at present.
In a world of environmental challenges, we really should be embracing it.”
The reprocessing of waste plastic into objects that add value in a home, office or other environment, is fundamentally simple. Plastic is a broad term for polymers, one of the most commonly known
and used worldwide being polyethylene terephthalate, or PET (think Coke bottles and the like). Another high-use polymer is high-density polyethylene, or HDPE, used for the likes of milk bottles, often opaque in appearance and not able to withstand temperatures as high as PET. Plastic waste has become an enormous environmental challenge due to its single-use nature and the fact that there is no ‘away’ when plastic is thrown away. However, Matt believes this is the point that needs
to be explored and the problem of single-use plastic is a behavioural one.
“Plastic is only described as single use because we use it once. But most plastic, including the widely used polymers, can be reprocessed and reused many times before they start to degrade.”
The advantages of repurposing waste polymers has significant ecological benefits, as well as reduced production times. 3D printing offers the ability to design specific fit-for-purpose items because design softwares allow for infinitesimal adjustments, and the option for designers such as Matt to create outside traditional constraints — a curve becomes as simple to create as a straight line, for example. “The freedom of this style of design and fabrication allows me to create beautiful shapes from waste that supersedes the original intent of the product it used to be.” An exciting addition to the range of homewares will include products designed collaboratively with digital fabrication designer Clark Bradsley, who has designed for international fashion giant, Cos.
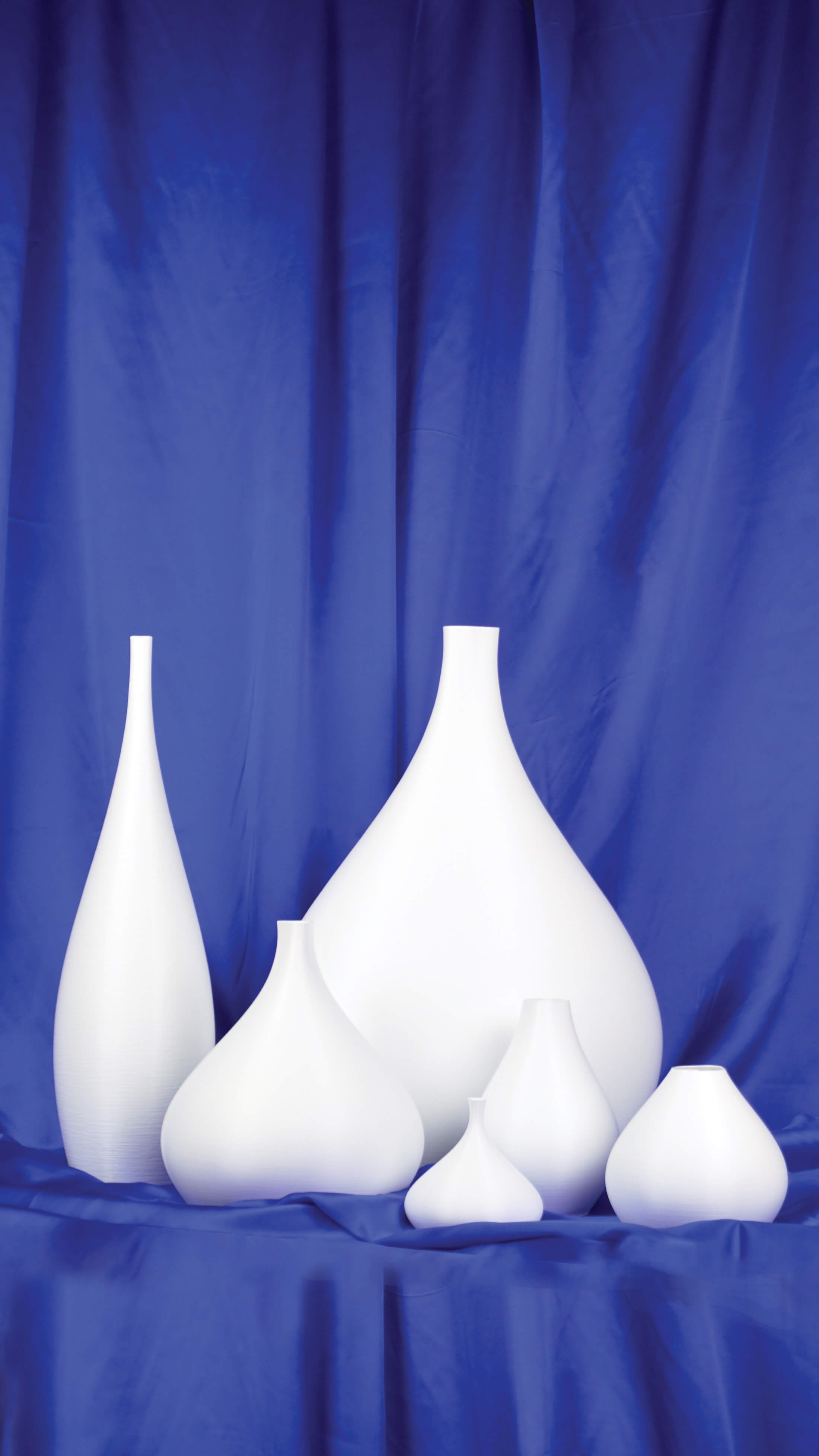
Incredibly, the sourcing of recycled filament is a challenge. There is a vast range of new polymer products to draw on, but sourcing usable recycled filament in New Zealand has sadly not been simple. In the meantime, Matt uses a range of filament from the two suppliers he has been able
to find in the Netherlands and the Czech Republic. Though he pays 30 to 40 times more for the product than it would cost to produce in-house, the overall cost and associated carbon footprint
is significantly better than using any filament produced locally with virgin polymers. The filament
is made from a variety of end-use products, some come coloured, some are combined with
other materials, such as marble dust, sea shells and various colourants. These additives change
the properties of the final composite product, contributing to weight, strength, flexibility, rigidity
and surface finish.
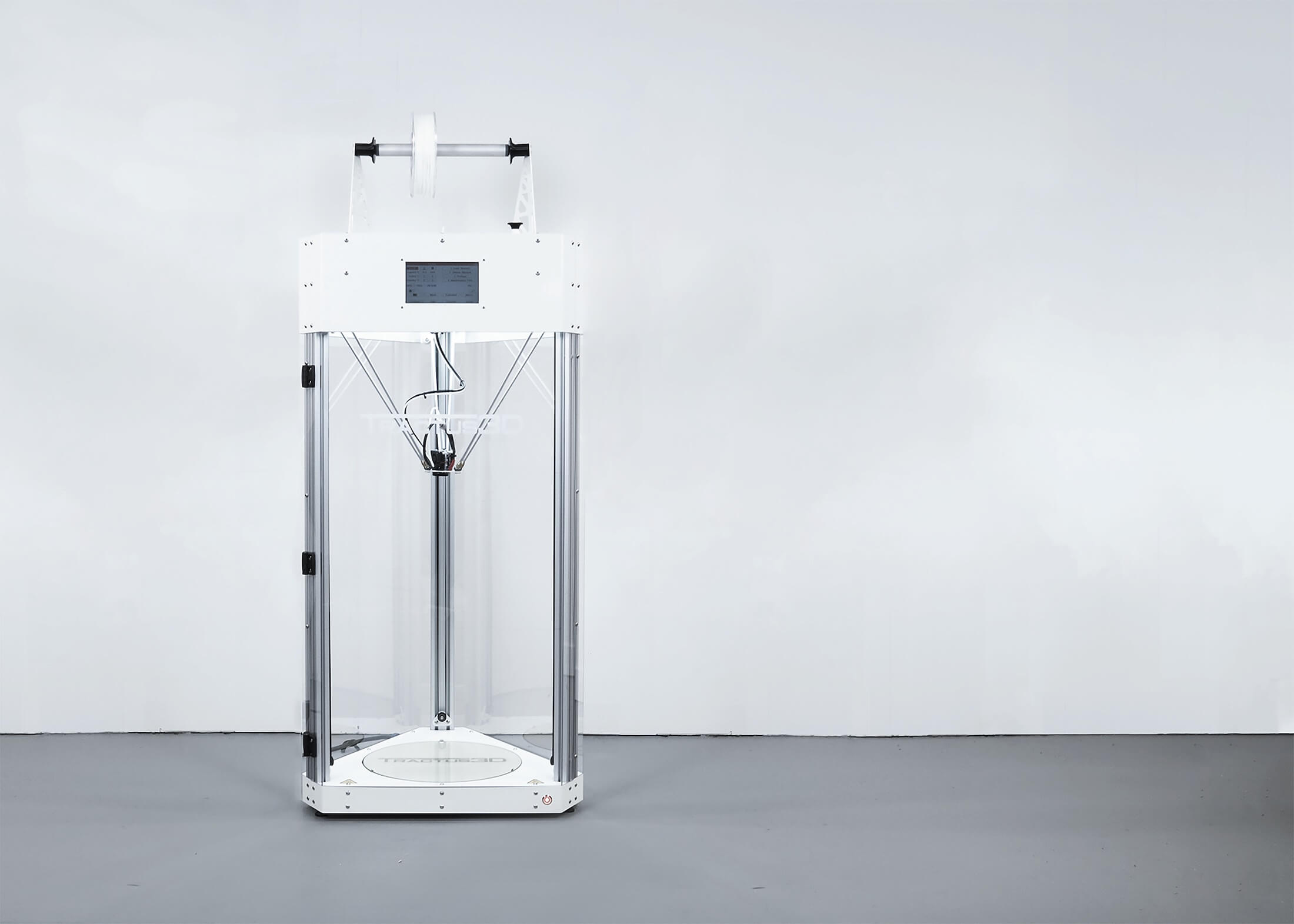
Preparing filament to be used in the 3D printing process is a simple, yet fickle one. Raw crushed plastic waste is ground in a machine not unlike a coffee grinder. The next stage involves removing moisture from the raw product and the now fine, dry, flaky product is converted into filament of a very precise diameter with a tolerance of +/-0.05mm. It’s these tolerances that require high precision processes and machinery. The filament is wound onto a spool that’s threaded into the printer,
a surprisingly simplistic device. The object being printed is coiled slowly and steadily into shape
of a design visible on an adjacent desktop computer.
Matt checks regularly on progress, though one of the most popular items for sale on Special Studio’s online store came about due to a design “fault”. “The mesh wastepaper basket happened because the filament was slightly too cold as it was printed and it ended up creating a mesh rather than
dense finish… It appealed to a number of people who have seen the sample, which can now be ordered in various sizes. We’re doing a limited run of it in emerald green too.”
If owning a unique, one-off item for your home is something that appeals, checkout the web store and be part of a bigger picture in the transformation of waste to value.